Fire Risk Assessment Guide & Checklist for the Motor Industry
Click here to download the print friendly checklist
This guide has been specifically written for all those that work in the motor industry or related environments, whether employers, employees, managers or owners. The motor industry is an umbrella term for a number of organisations involved in the creation of motor vehicles (from design through to manufacturing and marketing), but does not refer to the maintenance of cars and vans (such as garages that offer servicing and repairs, petrol stations etc.)
This guide is designed to offer specific fire safety advice to those operating within this industry, remaining in accordance with more universal regulations. It includes a tailored checklist to help make sure fire risk assessments are carried out correctly with specific reference to this field, as well as other ways in which your business can remain compliant with the law.
The Law
Whatever the nature of the business that you run, whether in the motor industry or otherwise, you are subject to the requirements of the Regulatory Reform (Fire Safety) Order 2005. This all-encompassing piece of legislation was introduced to replace over 70 disparate pieces of fire safety law in England and Wales, enforcing employers, landlords and business owners to take responsibility for the safety of their employees and visitors to the premises.
Under the guidelines of the Order, a ‘responsible person’ must be designated to take charge of all aspects of fire safety. This includes carrying out a fire risk assessment, ensuring that all fire detection and fighting equipment is correctly installed and maintained and keeping all staff informed of their duties in regards to evacuation procedure and upholding fire safety.
The risk assessment is one of the most important tasks allotted to the responsible person, allowing for the identification and removal of hazards and risks within the premises. In the motor industry environment, whether in a showroom forecourt or manufacturing plant, specific areas to look out for when carrying out your risk assessment include the prevalence and storage of combustible materials and flammable liquids, safe exit points that are clear of obstruction and correct use of spark-creating tools.
Conducting a Fire Risk Assessment – 5 Steps
Government recommendations suggest that there are five steps to consider when carrying out a fire risk assessment at your place of work.
It is also advised that you separate each area of your working environment into sections (office areas, forecourt, factory, warehouse etc.) to make the process easier.
#1 Identify the fire hazards
Making your way carefully around the area in question, make a note of any fire hazards you come across. Remember the fire triangle – the three elements that cause fire: a source of ignition, a source of oxygen, a source of fuel.
#2 Identify people at risk
Those at risk in your showroom or factory not only include every member of staff, but also customers and other visitors. Pay particular attention to those who may be more vulnerable when an evacuation is required. This includes those with a disability that impairs movement or the senses, the elderly and young children.
#3 Evaluate, remove and reduce the risks
Evaluating the information you have acquired in steps 1 and 2, action must now be taken to reduce or remove any hazards discovered.
This might entail fitting fire safety equipment, such as extinguishers, detection equipment, alarms, emergency lighting and signage, fire doors and more. If this is the case, standards must be met for quality of installation, and correct scheduling for periodic testing and inspection must be put in place.
#4 Record, plan, inform, instruct and train
Any hazards or issues that you discover are irrelevant if they are not recorded in some way. Be sure to keep an accurate log of your findings and actions, with individual records for each area within your motor industry organisation, making a note of all hazards encountered and steps taken as a result.
An evacuation plan to be carried out in the event of a blaze should also be created, and should be practiced on a regular basis. Your staff should be made aware of the plan, as well as be thoroughly trained on all fire safety procedures you implement.
#5 Review
Performing a fire risk assessment once is of little use. It must be regularly reviewed and updated wherever necessary.
Checklist
Keep the assessment simple and straightforward so that it is easy to execute. To help you do this, we’ve put together a handy checklist that should help you to comply with all government guidelines and regulations regarding fire safety in the motor industry.
#1 What are the fire hazards within your environment?
- This should include anything that is a source of ignition – i.e. welding equipment, machinery.
- It should also consider anything that is a source of fuel – i.e. flammable oils and solvents, combustible materials, compressed gases.
#2 Who is at risk within your environment?
- Note anyone within the environment who is particularly vulnerable – i.e. those with a disability, those working in loud conditions that may not hear an alarm, those working with hazardous materials and machinery.
#3 How will you keep people safe within your environment?
- Keep working areas tidy and free from obstruction.
- Pay special attention to the use and storage of combustible materials and flammable liquids/gases.
- Are oily rags and solvent brushes kept away from ignition?
- Is all waste being disposed of safely?
- Have waste collection services been put in place?
- Is the correct signage present throughout the building?
- Have all electric components (including lighting) undergone PAT testing?
- Is cleaning carried out on a regular basis to prevent oil spills etc. from being left untreated?
- Are all evacuation points kept clear of obstruction?
- Are the fire extinguishers present the ones most suited to the environment?
#4 Record, plan and train
- Take steps to remove or reduce each fire risk wherever possible.
- Record each step taken in your log.
- Those hazards that cannot be removed should be assigned a plan in order to rectify them.
- Detail a timeframe and schedule for executing all fire safety improvements.
- Ensure that all staff members in your showroom, office, warehouse or factory are fully trained and aware of their responsibilities during an emergency evacuation. Perform regular drills to achieve this.
- Similarly, make sure that all employees are familiar with the use of fire extinguishers, particularly which ones to use on which fire type.
- Finally, keep all of your logs and findings in a place that’s accessible to everyone on your premises, and be sure that all specific fire safety information (fire exits, assembly points, evacuation procedures, fire extinguisher types) is fully visible to all visitors.
#5 Review and maintain your plan
- If you make any interior or exterior alterations to your environment, then your fire risk assessment must be reviewed and amended as necessary.
- Any fires or near-misses should prompt a review of your plan.
- Any new equipment or working practices that are introduced to your premises will necessitate a review.
- All fire drills should be recorded and your plan updated accordingly.
Request a Callback
Just fill in your details below and we'll get back to you as soon as we can!
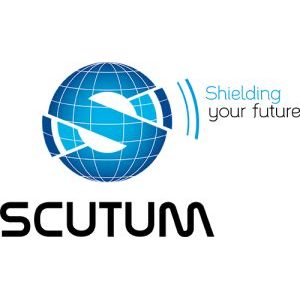
About Scutum London
Scutum London is a leading expert in fire safety and security solutions for businesses and organisations located across South East England, including London and Surrey.
From fire alarms, fire extinguishers and fire risk assessments to access control, CCTV and intruder alarm systems – and a lot more besides – we offer a comprehensive range of products and services designed to keep you, your business and your staff and visitors safe.
With decades of industry experience to call on, we’re proud to hold accreditations from leading trade associations and bodies such as British Approvals for Fire Equipment (BAFE), the British Fire Consortium, the Fire Industry Association (FIA) and Security Systems and Alarms Inspection Board (SSAIB).
If you’d like to find out more about Scutum London, get in touch with our friendly team or explore our products and services on our site.